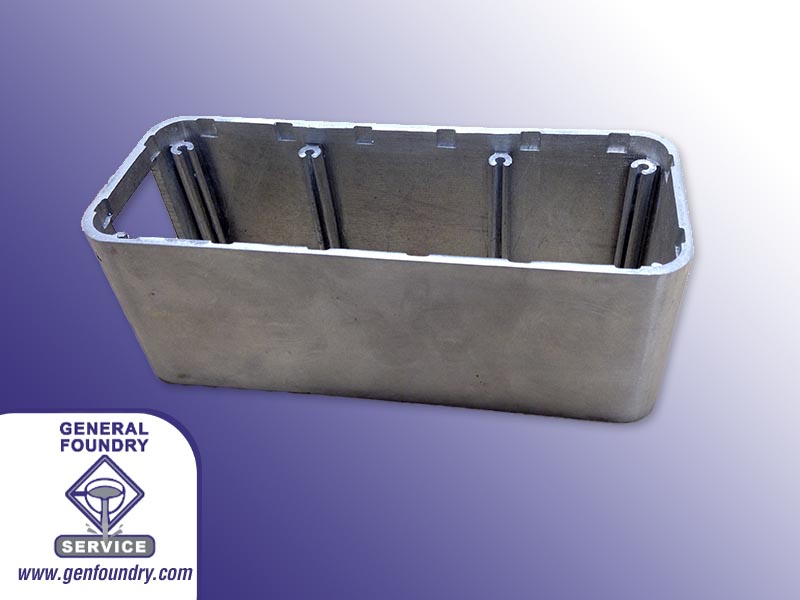
Investment Casting, also known as Lost Wax Casting, is a manufacturing process used to create metal parts by pouring molten metal into a mold made from a wax pattern. The term “Lost Wax Casting” comes from the fact that the wax pattern is melted away or “lost” during the casting process. The word “Investment Casting” comes from the solid plaster mold or ceramic shell used in the process, called an “investment.”
Investment or Lost Wax Casting is a highly precise process that allows for the creation of complex parts with tight tolerances and fine details. It is commonly used to manufacture parts for the aerospace, medical, and automotive industries, among others.
What is the Investment or Lost Wax Castings manufacturing process?
Parts manufactured utilizing this process will provide closer tolerances for your product’s design specifications. The Investment casting process starts with a pattern made from wax; these patterns are either created from a die or are 3D printed. Next, a flask is placed around the wax tree, and dense plaster slurry is poured into the flask, creating a solid mold. The wax is then melted out of the mold, leaving a cavity in the shape of the desired part. Under vacuum, molten metal is then poured into the cavity, and once the metal cools and solidifies, the plaster mold or ceramic shell is broken away to reveal the final part. Investment or Lost Wax casting provides tight ‘as cast’ tolerances and is the best casting technique for high detail ‘as cast’ applications. The mold used to create the wax patterns is reusable, but the solid mold or ceramic shells are broken and discarded after each production run.
Why select this process for your parts?
Investment or Lost Wax Castings offer several advantages over other casting processes, making them a good choice for many industries and projects.
Some of the main benefits of Investment or Lost Wax Castings include (but are not limited to):
- Increased Design Flexibility: This type of casting allows for the creation of complex parts with intricate shapes and fine details that may be difficult or impossible to achieve with other casting methods.
- High Precision, Tight Tolerances, & Greater Product Detail: The process produces parts with tight tolerances and excellent surface finishes, making it ideal for applications that require precision and accuracy.
- Versatility & Intricate Designs: This casting process can be used to produce parts in a wide range of sizes, from small intricate components to large complex parts.
- Wide Variety of Material Options: These castings can be created utilizing a variety of metals, including aluminum, stainless steel, titanium, and many more.
- Reduces Per-Part Machining Costs: These castings can seem a bit pricey; however, they can save you quite a bit on secondary machining processes as the cost of tooling is relatively low compared to other casting methods.
What are some common industries and applications for Investment or Lost Wax Castings?
Investment or Lost Wax Castings produce highly detailed components used for a wide variety of industrial applications worldwide. These industries require manufactured products that provide strength, reliability, and extremely precise tolerances.
Some of the industries that commonly utilize Investment or Lost Wax Castings include (but are not limited to):
- Aerospace
- Biotech and Life Sciences
- Electronics
- Jewelry Making
- Medical Equipment
- Military and Defense
- Robotics
- Sculpture
- Semiconductor
- And many more
Investment or Lost Wax Castings can provide a highly precise and flexible manufacturing option that can be cost-effective for small production runs and offer versatility in terms of materials and design.
How can General Foundry Service help you?
Investment or Lost Wax Castings provide our customers with the most design freedom, thinnest walls, tightest ‘as cast’ tolerances and the highest ‘as cast’ details possible. This process tends to be a bit more expensive at the front end, but the overall value provides benefits that other processes cannot match. Lost wax castings reduce the machining portion of the total per-part cost, which can lead to less money spent on other aspects of part production. General Foundry Service offers true one-stop shopping. With our in-house pattern shop, machine shop, and five complementary casting processes, we specialize in machined, Class A, cosmetically coated aluminum castings to a Class A finish. Contact us today for more information about our clean metal casting solutions or to get started on your next project