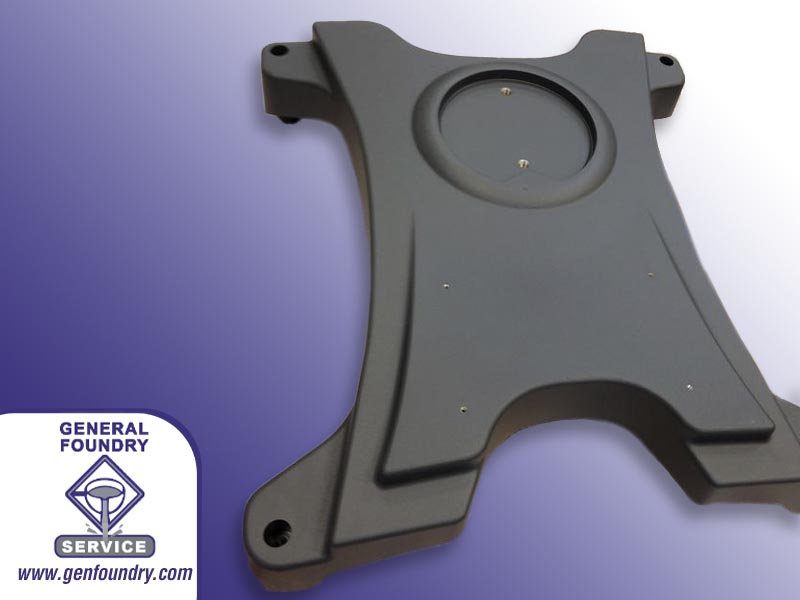
No bake (air set) sand casting provides a versatile option for metal casting. This process can produce parts and components in various shapes and sizes. The rigid molds made for an air set sand casting provide good dimensional tolerances and control. No bake (air set) sand castings are similar to green sand castings, but in this process the sand is chemically bonded, producing a more dimensionally stable and accurate mold. This process is ideal for larger (100 pound plus) and more complex shaped (deep draw) castings.
How Does No Bake (air set) Sand Casting Work?
As stated above, this process is very similar to green sand casting with two major differences – this process uses chemically enhanced sand and split out cope and drag style tooling. The no bake (air set) sand casting process utilizes chemical binders to bond the molding sand; meaning the sand is mixed with a binder and a catalyst. As the sand exits the mixer, the binder begins the chemical process of hardening. A rollover is then used to remove the mold halves from the positive tool.
The process can be further broken down into the following steps:
- A pattern is made of wood, plastic, metal, or other material.
- Create no bake sand cores (if needed).
- Chemically enhanced sand is compacted against the positive patterns on the cope and drag tools.
- The sand sets for 20-30 minutes.
- Remove mold halves from tool.
- Insert any cores in mold halves (creating undercuts and/or hollow features).
- Close mold halves on top of each other, and pour molten metal into the mold cavity.
- The casting cools and solidifies.
- The mold is broken open and the casting removed (shake out process).finally opened and the sand is removed from the newly formed solid metal geometry.
What are the advantages of no bake (air set) sand casting?
There are many distinct advantages to no bake (air set) sand casting over other casting processes. The no bake (air set) process is ideal for creating large, high-value, heavy, and critical castings.
Some of the benefits of utilizing no bake (air set) sand castings, include (but are not limited to):
- The sand can be reclaimed and recycled.
- It offers an efficient and repeatable process to manufacture large geometries and heavy or intricate castings.
- The process is versatile and can accommodate a wide range of castings, from small to extra large.
- Big castings can be made in a single mold.
- It can reduce BOM costs by combining multiple pieces into one cast part.
- The process creates castings with a smooth 150 RMS surface finish.
- And more.
What size and part complexity does this process offer?
The no bake process is most often used to create large and complex cast geometries. The thinnest wall section (geometry dependent) for a no bake (air set) sand casting is 0.125”, most thin-walled components will be made closer to 0.160” and larger geometries at 0.200” or thicker. This is General Foundry’s largest envelope-size process, creating shapes up to 6 feet in diameter by 4 feet deep and up to 500 pounds in weight.
No bake (air set) sand casting is a versatile process that can be used to produce a variety of castings. Due to the large size, smooth surface finish, and intricate or complex part capabilities it is a great choice for a variety of industries including the production of medical device cart bases, life science/biotech instrument bases, a variety of robotic parts, defense applications, large heat sink applications and a variety of other industrial components.
How can General Foundry Service help you?
General Foundry Service is an industry-leading provider of aluminum and zinc aluminum coated and machined castings. We can produce a wide range of parts, components, and products utilizing our no bake (air set) sand casting process. We have the capabilities to produce the parts and components that you need with short lead times. Our metal casting experts will work with you to design and develop your no bake (air set) sand casting based on your unique specifications and project requirements.
General Foundry Service offers true one-stop shopping. With our in-house pattern shop, machine shop, and five complementary casting processes, we specialize in machined, Class A, cosmetically coated aluminum castings. Contact us today for more information or to get started on your next project.