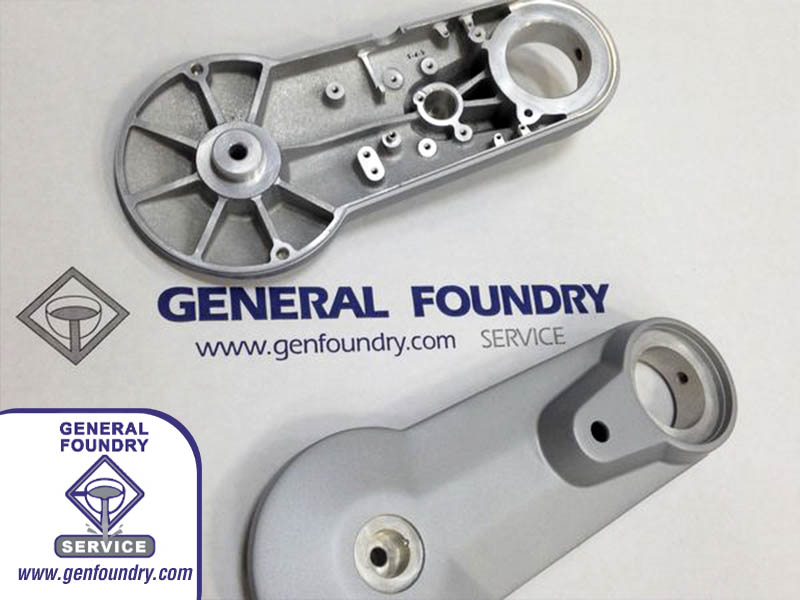
According to a recent Markets and Markets report, the global market for medical device manufacturing is expected to reach $56.2 billion by 2025. Metal castings stand as a cornerstone technique in medical device manufacturing. Engineers navigating this specialized field face the challenge of balancing innovation with precision while meeting stringent regulatory standards. From life-saving pacemakers and advanced joint replacements to medical capital equipment, metal casting plays an indispensable role.
Sand casting, in particular, is a versatile and cost-effective manufacturing process for producing a wide range of metal components, especially parts for medical devices. While sand casting may not be suitable for all medical device applications, it can be a viable option for specific components that require custom shapes or low to moderate production volumes.
Sand casting involves the use of sand molds to create metal parts. It is a relatively simple and flexible method for producing complex shapes and is the most cost-effective process for low to moderate production quantities. This casting type is incredibly valuable for prototyping new medical device components and creating custom parts before committing to mass production. Sand casting is used to produce a variety of medical device components, including:
- Braces and supports
- Custom instruments
- Handles, carts, and housings
- Robotic components
- And more
However, not all medical devices are suitable for the sand casting process. Medical devices have a zero margin for error as lives may be on the line. A single imperfection can compromise the device’s functionality. There are many factors to consider when selecting the process for your next medical component, such as the complexity of the part, required tolerances, the material desired, production volume, lead time, costs, and more.
The choice of material is often critical in medical device manufacturing. Navigating the complex landscape of FDA guidelines and other regulatory requirements is a must for any engineer in the medical device field. When selecting materials, you must consider their physical and chemical properties and how they comply with healthcare regulations.
Common materials used in sand casting for medical devices include (but are not limited to):
- Aluminum 356 (great strength to weight ratio)
- AlMag 535 Aluminum Magnesium (increased elongation value for higher factors of safety)
- ZA8 Zinc Aluminum 8 (2.25x the density of 356 for heavier ballast bases, lower COG)
Material selection should align with the specific requirements of the medical device, such as biocompatibility, strength, and wear resistance. The parts likely will also require additional post-cast processing (secondary), such as:
- Heat treatment: To enhance material properties.
- Machining: To achieve precise dimensions.
- Surface finishing: For aesthetics and chemical resistance.
The medical device industry is one of the most heavily regulated sectors, and for good reason. Components must meet rigorous standards to ensure they are safe and effective for patient use. Quality control is paramount in medical device manufacturing. Sand casting for medical devices must adhere to strict quality standards and validation processes. This includes inspection, testing, and documentation to ensure the final product meets print.
Sand casting can be a viable manufacturing method for certain medical device components, especially those with custom shapes and moderate production volumes. However, it is crucial to consider material selection, quality control, regulatory compliance, and post-casting processing to produce safe and reliable medical devices. Always consult with experts like General Foundry Service to ensure the best possible components for your specific medical device application.
How can General Foundry Service help you?
With 70 years of casting experience in the medical industry, General Foundry provides a “get it right the first time” quality and customer-focused approach. With an expert staff that has produced thousands of medical device components, General Foundry provides a best-in-class turnkey solution with multiple processes and alloy options to meet your medical component casting needs. Contact us today for more information about our clean metal casting solutions or to get started on your next project.