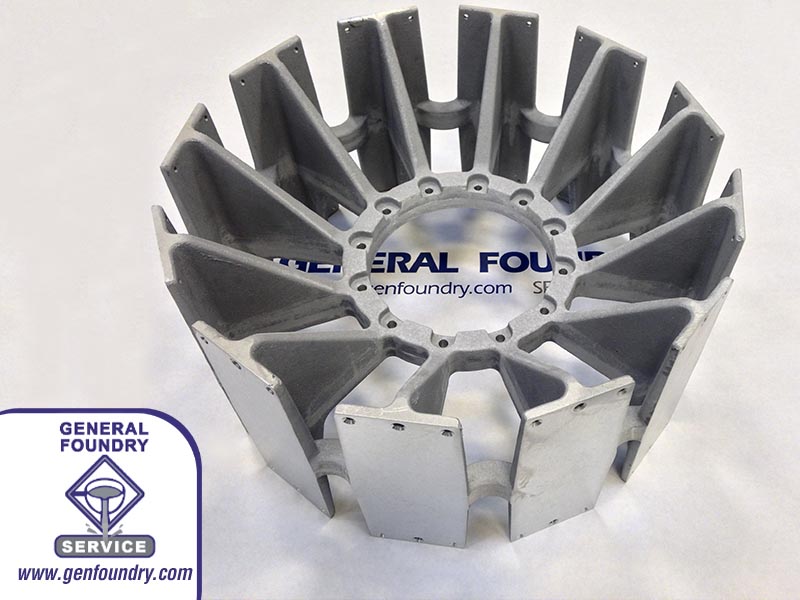
Metal casting techniques help push the boundaries of healthcare technology, making medical devices more effective, reliable, and accessible. They also play an indispensable role in driving worldwide medical device manufacturing. Engineers navigating this specialized field face the challenge of balancing innovation with precision while meeting stringent cost targets and regulatory standards. Metal castings can play a critical role in these goals and healthcare advancements.
Aluminum Casting Processes for Medical Device Components
Understanding the different metal casting processes available is helpful for any engineer in the medical device industry.
There are various low-volume casting methods to choose from, including:
- Sand casting (green and no-bake sand)
- Rubber plaster mold casting
- Investment casting
- Permanent mold casting
The choice of method depends on several factors, including the complexity of the design, tolerances that must be held, and the required material for the part. For example, investment casting is often used for intricate medical device instruments or implant components due to its ability to produce fine details, complex geometries, and ferrous alloy options. Sand casting is suitable for a wide range of geometries, including simple curvy cosmetic handles, larger device base geometries, structural hollow complex parts, or basic cable cord wraps. Rubber plaster mold castings should be utilized for thinner wall geometries (down to 0.080” nominal walls), such as robotic arms or links, hand-held devices, some instrument holders, heat sink applications, and thin-walled covers. Permanent mold parts have increased mechanical properties and increased tooling costs meant for higher volume (2000+) applications, like dental chair components.
Medical devices often have a zero margin for error. They must be highly accurate, durable, and consistent. All those critical-to-function dimensions should be secondarily machined for high accuracy and repeatability. Medical devices are often used and sterilized repeatedly. This makes their durability a significant factor in the long-term success of a medical device project. Aluminum, by itself, is already corrosion resistant, but adding a chemical chromate followed by a cosmetic powder coating or liquid paint will not only create a cosmetic geometry, it will also help seal the casting to withstand stringent repeated cleaning and sterilization. Attention to detail at every stage of the casting process is imperative to meet varying requirements.
Selecting the Right Material: More Than Just Casting
Medical devices require materials with specific properties, such as biocompatibility, corrosion resistance, and strength. When selecting materials, you must consider their physical and chemical properties and how they comply with healthcare regulations. This is especially true for devices that will have prolonged contact with the body. Safety factors are top of mind when designing parts in the medical device realm. With high elongation material properties, aluminum magnesium 535 (almag) can provide a good solution. A356 aluminum is another option that offers excellent strength-to-weight ratio. Finally, many device designers want a low center of gravity or a ballast effect in or on the device cart base. Zinc aluminum 8 (ZA8), offers a much denser alloy option. At 92% zinc and 8% aluminum, it is 2.25x the density of A356 aluminum. Instead of dropping in a steel or iron plate, designing base components out of ZA8 results in higher-value components and saved assembly & BOM costs.
Optimal Surface Finish Considerations
General Foundry Service routinely delivers cosmetically coated class A medical device aluminum castings with powder coating or liquid painting. Especially with sand castings, there exists a stigma that they cannot be cosmetic. General Foundry is breaking this falsehood daily by focusing on three key foundry quality metrics: smooth machined plastic or aluminum foundry tooling, clean metal through our degassing standard, and ultra-fine grain olivine sand. This provides an industry-leading 125 RMS and a great head start for our coaters to achieve a smooth or textured cosmetically coated surface finish. Smooth silver is among the most popular, the Steve Job’s look: anodized aluminum. This is the most expensive and least forgiving to achieve. A texture helps hide the casting’s flaws and is more economical. Coating a casting is like painting a car, there are several prep steps that must be followed to achieve the desired outcome. One of General Foundry’s core competencies is creating cosmetically coated class A medical device components.
A Peek Into Quality Control: Ensuring Reliability
The medical industry demands a high level of precision and quality control to ensure the safety and efficacy of devices. In a field where a slight error can have severe consequences, including loss of life, stringent quality control practices in casting parts are paramount. While each device may require specialized testing, there are some standard tests that almost all medical devices go through. These include, but are not limited to:
- Dimensional accuracy checks
- Material composition analysis
- Non-destructive testing (x-ray)
- Destructive material property tests
The goal is to catch any anomalies that could compromise the device’s performance or patient safety. Engineers have a hands-on role in quality control, from the design stage through to final inspections. It’s not enough to rely solely on automated tests or quality assurance protocols. Engineers must understand the unique medical device casting variables and how these can impact quality. Advancements in technology, such as 3D scanning and computational simulations, offer engineers additional layers of quality control. These tools can identify issues that may not be visible to the human eye, ensuring an even higher level of precision in medical casting and molding.
Navigating Regulatory Agencies: What Engineers Should Know
The medical device industry is one of the most heavily regulated sectors, and for good reason. Medical device manufacturers must adhere to regulatory frameworks such as the U.S. Food and Drug Administration (FDA) guidelines and international standards like ISO 13485. These guidelines directly affect medical device casting, covering everything from material selection to quality control protocols. Compliance with these regulations is crucial to ensure patient safety and product quality.
Metal casting is an integral process in the production of medical devices. This manufacturing technique enables the creation of precise and customized components from biocompatible materials, with a strong focus on quality control and regulatory compliance to ensure the safety and effectiveness of medical devices in healthcare applications.
How can General Foundry Service help you?
With over 70 years of casting experience in the medical industry, General Foundry provides a “get it right the first time” quality and customer-focused approach. With an expert staff that has produced thousands of medical device components, General Foundry provides a best-in-class turnkey solution with multiple processes and alloy options to meet your medical component casting needs. Contact us today for more information about our clean metal casting solutions or to get started on your next project.