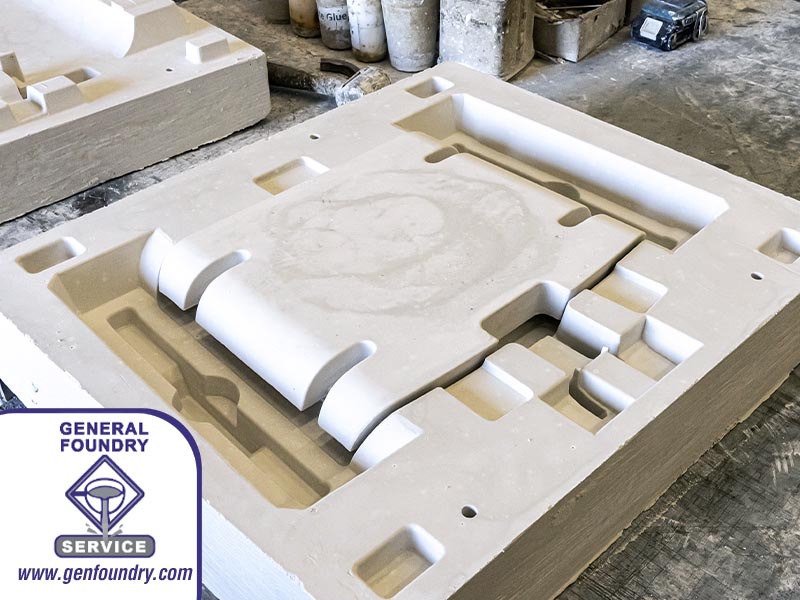
Despite facing challenges such as fluctuating raw material costs and stringent environmental regulations, the casting industry’s future looks promising thanks to ongoing innovations by industry leaders such as General Foundry Service.
The margin for error is practically non-existent in just about every sector, and this is where rubber plaster mold casting shines. Rubber Plaster Mold (RPM) casting is a specialized prototype and low-volume production process that provides a complementary alternative to investment casting, sand casting & die casting. The method is well known for delivering parts that meet or exceed even the most stringent quality standards.
Why is this technique becoming the go-to option for companies seeking unparalleled precision and efficiency? Let’s explore the advantages of Rubber Plaster Mold casting and how this process drives innovation in some of the most advanced engineering and design fields.
1. Superior Precision and Detail
Rubber Plaster Mold casting offers higher levels of precision and detail than other processes, such as green sand casting, making it a favored technique in various industries. By utilizing plaster molds, manufacturers can achieve intricate designs and precise dimensions that surpass those possible with other casting methods. The fine texture of plaster allows for exceptional reproduction of even the most delicate features, ensuring that each component meets exact specifications. These molds can be easily modified to accommodate design changes, enabling flexibility throughout production without sacrificing precision. This level of detail is crucial in industries where accuracy is paramount, such as aerospace, telecom, robotics, and medical device manufacturing.
2. Versatility Across Industries
RPM casting boasts remarkable versatility across industries, making it a cornerstone technique for crafting components and driving innovation in diverse applications, such as medical tools, parts for robots, or telecom devices. RPM casting enables the production of complex shapes with exceptional detail and accuracy. Its compatibility with a wide range of materials further enhances its versatility, ensuring it remains a preferred choice for manufacturers seeking reliable and efficient methods for component production.
3. Compatibility with High-Performance Materials
RPM casting is compatible with various high-performance materials, making it ideal for producing precision parts. For example, zinc alloys are frequently used for complex, intricate components due to the alloy’s good dimensional stability and high detail resolution. Aluminum alloys are commonly selected to cast lightweight, high-strength parts with excellent thermal conductivity. These high-performance materials, among others, allow RPM casting to produce detailed, precision parts that are strong, durable, and suitable for demanding applications across various industries.
4. Cost-Effectiveness
RPM casting offers significant value due to its enhanced part finish and detail compared to other casting methods, such as green sand casting. The rubber plaster molds used in RPM casting capture intricate details with greater precision, resulting in smoother surfaces and more accurate dimensions. This reduces the need for additional secondary machining and finishing processes, lowering labor and material costs. The reusable nature of rubber molds and their ability to produce fine, complex parts help streamline production and minimize waste, making RPM casting a cost-effective solution for precision components in industries requiring high-quality finishes, such as aerospace, electronics, and medical devices.
5. Quick Turnaround Time
The flexibility and resilience of rubber molds allow for quick creation and replication of intricate designs, significantly reducing lead times compared to alternative techniques. Moreover, the fast curing time of plaster further accelerates the production process, enabling manufacturers to swiftly produce high-quality components without compromising on precision or detail. This expedited turnaround time is invaluable in industries where time-to-market is critical, such as prototyping, product development, or short-run production cycles. By harnessing the rapid capabilities of rubber plaster mold casting, manufacturers can efficiently meet tight deadlines and respond promptly to market demands, ensuring competitiveness and agility in today’s fast-paced manufacturing landscape.
6. Environmental Friendliness
In an era where sustainability is increasingly essential, RPM casting stands out as an environmentally friendly manufacturing method, offering several sustainability benefits throughout the production process. The plaster material used in this process is non-toxic and biodegradable, posing minimal environmental risk during disposal. Also, the simplicity and energy efficiency of rubber plaster mold casting contributes to its eco-friendliness since it requires less energy compared to more complex manufacturing methods.
7. Excellent Surface Finish
RPM casting allows manufacturers to achieve an excellent surface finish on components, meeting the highest aesthetic appeal and functional performance standards. The inherent flexibility and resilience of rubber molds enable them to faithfully replicate intricate details and textures from the master pattern onto the cast components. This results in smooth surfaces, sharp edges, and fine details that rival those achieved through more expensive and time-consuming methods. The fine texture of plaster further enhances the surface finish, providing a uniform and flawless appearance to the final product. This is particularly beneficial for industries where the aesthetic quality of components is essential. A smoother surface adds value and refinement to the end product, enhancing its overall quality and appeal and improving the performance of parts by minimizing friction and wear, which is crucial in precision applications.
8. Reduced Need for Secondary Operations
RPM casting minimizes the need for secondary operations, streamlining the production process and reducing costs while maintaining high-quality results. RPM casting produces components with excellent surface finish and detail directly from the mold. The flexibility and resilience of rubber molds allow for precise replication of intricate designs, minimizing the occurrence of defects or imperfections that would necessitate post-casting adjustments. The fine texture of plaster further enhances the surface quality of the cast components, reducing the need for additional smoothing or refining. This efficient production method saves time and resources by eliminating the requirement for labor-intensive secondary operations, enabling manufacturers to deliver finished components more quickly and cost-effectively. For sectors like aerospace or defense, where each part’s integrity and performance are critical, producing near-net-shape parts that require minimal finishing is a significant advantage.
9. Enhanced Design Flexibility
RPM casting offers engineers enhanced design flexibility, empowering them to realize even the most complex and intricate component designs with precision and efficiency. The inherent flexibility of rubber molds allows for the creation of molds from various master patterns, including prototypes, CAD models, or existing components, enabling manufacturers to adapt quickly to design changes or customizations. This versatility extends to producing components with intricate geometries, fine details, and complex shapes that may be challenging or impractical to achieve using other manufacturing methods. The ability to easily modify rubber molds facilitates rapid prototyping and iterative design processes, allowing for faster innovation and product development cycles. This ability to quickly and efficiently produce complex designs is invaluable for industries developing cutting-edge technologies. It supports innovation and allows for the exploration of new concepts and solutions.
Manufacturing the Future
RPM casting empowers engineers to push the boundaries of creativity and innovation. It brings their visions to life, combining precision, versatility, and efficiency with smooth surfaces and sharp edges straight from the mold. It caters to the rigorous demands of various industries ranging from aerospace to telecommunications, offering innovative and reliable solutions. General Foundry Service emerges as your partner of choice for those seeking to leverage these benefits. With a solid foundation of innovation since 1946, our unique blend of experience, expertise, and commitment to quality and service position us to meet your most challenging manufacturing needs.
Watch this process in action!
How can General Foundry Service help you?
General Foundry Service is an industry-leading provider of aluminum and zinc aluminum coated and machined castings. We have the capabilities to produce the parts and components that you need with short lead times. Our metal casting experts will work with you to design and develop your casting based on your unique specifications and project requirements.
General Foundry Service offers true one-stop shopping. With our in-house pattern shop, machine shop, and five complementary casting processes, we specialize in machined, Class A cosmetically coated aluminum castings. Contact us today for more information or to get started on your next project.