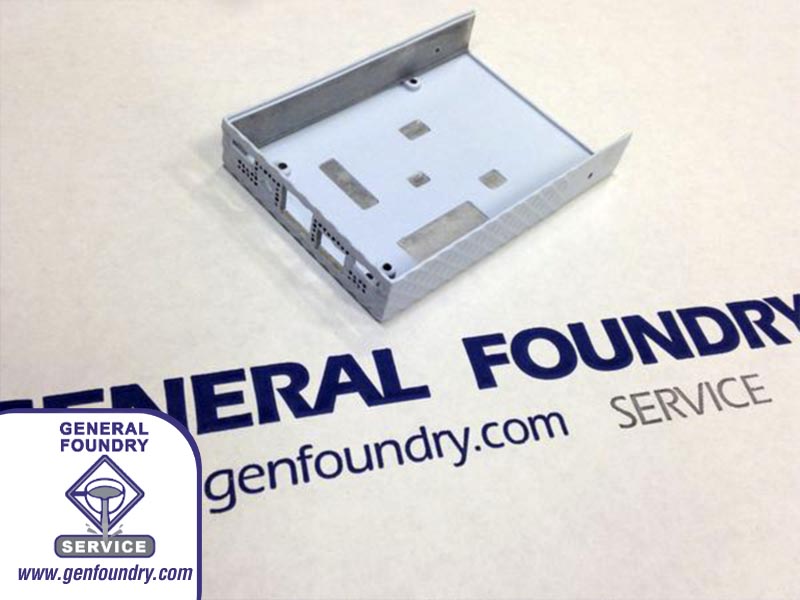
Investment (Lost Wax) Casting is a fantastic choice for engineers seeking efficient and precise manufacturing solutions. The process is well known for producing highly complex and accurate geometries; this versatile process addresses common pain points in engineering design and production. From reducing part count to offering extensive material options, investment casting empowers engineers to create high-performance components while cutting costs and lead times.
Before we begin, investment casting does have some practical size limitations. While it can produce parts of various sizes, it excels in a particular “sweet spot” where it offers the best balance of precision, cost, and feasibility.
Sweet Spot for Investment Casting:
- Weight: Typically, 0.1 to 10 lbs (50 g to 4.5 kg) is ideal.
- Size: Generally, parts under 8 inches (200 mm) in length are most efficient.
- Wall Thickness: Works best between 0.060 to 0.250 inches (1.5 to 6 mm), but can go thinner or thicker depending on the alloy and design.
Limitations & Practical Considerations:
- Larger Parts: Investment casting can technically handle up to 100 lbs (45 kg) or more, but costs and process challenges increase.
- Fine Detail & Complex Geometry: It is best for intricate parts where machining or other casting methods would be too costly.
- Material Constraints: Though m metals can be used, General Foundry Service pours 356, 357, 535 & ZA-8 alloys.
- Shrinkage & Warping: Larger parts are more prone to dimensional instability during solidification.
If you are considering investment casting, the best approach is to consult with an experienced foundry, such as General Foundry Service, to confirm if your design falls within optimal parameters.
With that in mind, here are 10 essential tips that highlight how investment casting can enhance your engineering projects, solve challenges, and deliver fantastic results:
1. Design Freedom for Complex Geometries
- Tip: Investment casting allows for intricate shapes and complex geometries that other methods can’t achieve without secondary processing.
- Pain Point Solved: Reduces the need for costly post-machining or assembly of multiple parts, saving both time and money.
2. Tight Tolerances for Precision Components
- Tip: The process provides excellent dimensional accuracy, often holding tolerances as tight as ±0.005 inches per inch.
- Pain Point Solved: Engineers can meet strict specifications without expensive secondary processes.
3. Material Selection
- Tip: Investment casting provides an extensive range of material options, with aluminum and zinc aluminum standing out for their lightweight properties, corrosion resistance, and versatility. These alloys are ideal for applications where weight reduction and durability are critical.
- Pain Point Solved: Engineers can tailor their material choices to meet specific application requirements, leveraging aluminum and zinc aluminum for optimal performance while having access to other alloys for high-temperature or specialized conditions.
4. High Strength-to-Weight Ratio
- Tip: Investment casting creates lightweight parts without sacrificing strength or durability.
- Pain Point Solved: Ideal for aerospace, automotive, and other industries needing lightweight but strong components.
5. Reduction in Part Count
- Tip: Complex designs can be consolidated into a single cast part, reducing the need for assemblies.
- Pain Point Solved: Simplifies assembly processes, reduces potential failure points, and lowers overall production costs.
6. Smooth Surface Finishes
- Tip: Investment casting produces parts with near-net shape and smooth surface finishes, often requiring minimal finishing work.
- Pain Point Solved: Saves time and cost in surface treatments while delivering a professional appearance.
7. Prototyping and Scalability
- Tip: Rapid prototyping with investment casting can help engineers test designs before committing to mass production.
- Pain Point Solved: Reduces risk of design flaws, enabling quicker iterations and faster time-to-market.
8. Excellent Reproducibility
- Tip: Investment casting ensures consistent quality across large production runs.
- Pain Point Solved: Engineers can rely on uniform performance for critical applications, such as medical and industrial equipment.
9. Cost Savings in Tooling
- Tip: Investment casting typically uses cost-effective, reusable wax patterns for tooling.
- Pain Point Solved: Reduces upfront costs compared to CNC machining or die-casting methods.
10. Environmental Sustainability
- Tip: The process recycles wax and wastes less material than other manufacturing methods.
- Pain Point Solved: Helps engineers meet sustainability goals and reduce their project’s environmental impact.
Investment casting is more than just a manufacturing process—it is a strategic solution for engineers looking to overcome design, material, and production challenges. Its ability to deliver precision, scalability, and cost-effectiveness makes it an invaluable tool for various industries. By leveraging the insights, engineers can unlock the full potential of investment casting to streamline production, enhance component performance, and achieve long-term success. Whether you are designing for medical, robotics, semiconductor, telecom, or other industrial applications, investment casting provides the flexibility and reliability to turn your vision into reality.
How can General Foundry Service help you?
With over 90 years of casting experience in various critical industries, General Foundry provides you with “get it right the first time” quality and a genuinely customer-focused approach to each project. We offer best-in-class turnkey solutions with multiple processes and alloy options to meet your component casting needs. Contact us today for more information or to get started on your next project.