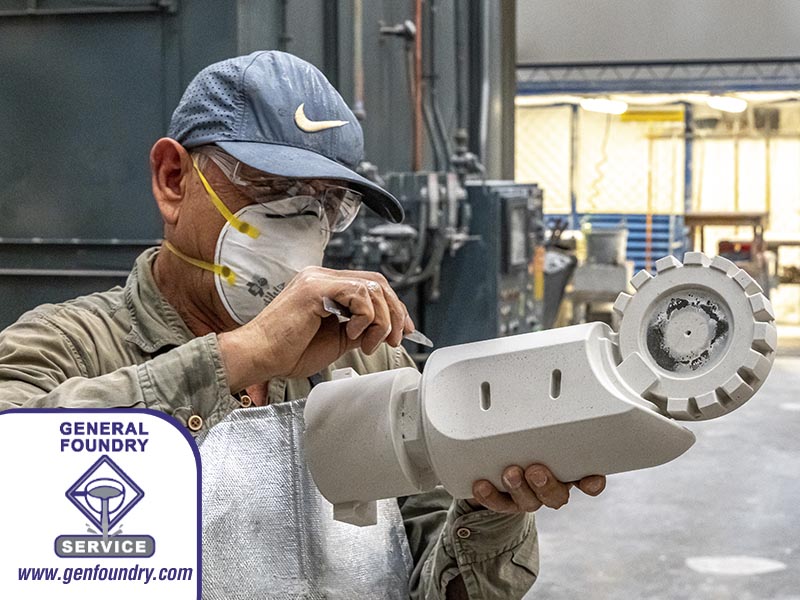
The medical technology market is on track to reach an impressive $31.58 billion by 2030. This surge signifies a leap in the need for better medical and surgical equipment. These trends are pivotal for engineers in life sciences as technology and innovative engineering continue to revolutionize medical industries. Medical innovations are shaping the future of healthcare and redefining the medical landscape, showcasing a remarkable fusion of engineering skills and life-saving innovation.
Advanced Materials in Surgical Equipment
Driven by advancements in material science, we are witnessing remarkable transformations in medical devices, technology, and treatments. Cutting-edge materials, ranging from bio-compatible metal alloys to advanced polymers, are setting new standards in medical devices. These materials are more durable, efficient, and safer for patients. Casting alloys and metallurgy play crucial roles in this innovation, as medical practitioners and surgeons today require lighter, stronger, and more responsive tools.
Robotics and Electromechanical Systems in Surgical Developments
Surgical robotics is a field currently experiencing innovation and rapid growth. From enhanced sensors to AI integration, the capabilities of surgical robots are expanding. These systems offer unprecedented precision and control, changing how surgeries are performed. Robots can execute complex procedures with minimal invasiveness when guided by an expert hand, increasing positive surgical outcomes, and speeding up the patients’ procedure and recovery time. This lowers the overall costs for patients as well.
Precision Components Enabling AI in Surgical Equipment
The medical field’s future with AI integration is promising and demands close collaboration to craft the necessary highly precise electronics and metal components; these include sensor housings and robotic interfaces, where exact standards are non-negotiable. Engineers face the complex task of designing hardware that aligns perfectly with medical needs, patient needs, AI technology integration, and manufacturability.
Enhanced Connectivity in Medical Innovations
The trend of interconnected surgical tools is reshaping modern healthcare. Paired with new AI technologies, IoT-enabled devices in surgery offer real-time collaboration, data, and improved patient monitoring. This evolving landscape of connectivity demands robust and reliable components. For engineers, the challenge lies in integrating this connectivity with precision, ensuring every component functions flawlessly within the network.
Precision Metal Casting
The medical-surgical equipment sector faces challenges and opportunities with the next generation of medical tools demanding even greater precision, integration with digital technologies, and material innovation. Aluminum and zinc aluminum castings, made from the sand casting process, the rubber plaster mold process, or investment castings can be excellent economic alternatives to machined components or die-castings. Many medical device bases and handles, surgical tools, robotic arm parts, electromechanical enclosures, and cord wraps are great casting candidates. Further, these processes are particularly advantageous for producing intricate shapes and detailed designs required in components such as robotic arms, joint mechanisms, other sophisticated parts used in surgical robots, AI-driven surgical tools, as well as parts involved in motion control, sensor housing, and other critical functionalities.
For example, aluminum, known for its excellent strength-to-weight ratio, results in lightweight instruments that reduce surgeon fatigue while maintaining durability for repeated use. Both aluminum and zinc offer excellent corrosion resistance, crucial for maintaining sterility and safety over time, even after frequent sterilization; their biocompatibility ensures that instruments are safe for contact with the human body, minimizing the risk of adverse reactions.
Metal casting processes are ideal for product development and rapid prototyping because they help keep overall costs low. For example, companies can start with a casting from 3D-printed sand molds for prototyping, allowing for quick design iterations at a lower cost. Once the design is finalized, they can transition to other casting methods for higher-volume production, making the process both efficient and economical throughout the product lifecycle.
How can General Foundry Service help you?
With almost 80 years of casting experience, General Foundry provides a “get it right the first time” quality and customer-focused approach. With an expert staff that has produced thousands of medical device components, General Foundry provides a best-in-class turnkey solution with multiple processes and alloy options to meet your medical or surgical component casting needs. Contact us today for more information about our metal casting solutions or to get started on your next project.